Wet insulation can cause many building problems, from structural integrity damage to issues of energy efficiency and occupant health. Wet insulation is often in contact with steel structural members in commercial buildings. Structural damage occurs from rusted steel studs, corroded wall ties, and screws that hold the ties being continually wet. “Over time, loosened ties result in excess movement, which leads to cracked and discolored wall surfaces; in the worst cases, it even leads to partial collapse of veneer wall systems,” says Ried Artis, public relations leader for Owens Corning’s building materials group.
Loss of thermal performance is another consequence. If insulation is wet it becomes a conductor of energy. When insulation conducts energy rather than reflects it, it results in higher heating or cooling bills. In winter for example, heat rises from the heaters; that heat goes through the ceiling of the roof and you lose that energy. If you have insulation on the top, the heat reflects back down so you’re conserving energy.
Moisture caused by wet insulation contributes to mold. Mold needs mold spores, a food source, adequate temperature, and moisture to thrive; water is often the only element that can be controlled. If we control and limit water in the wall by using good design, good construction, and good maintenance, there’s a decent chance of controlling mold growth.
Consequences of Wet Insulation
- Roof leaks can cause costly interior damage to facilities and create hazardous conditions for building occupants.
- Wet insulation becomes a conductor of energy rather than a resister, resulting in increased energy bills.
- Trapped moisture in insulation is a great place for mold to thrive and may eventually lead to indoor air quality issues.
- Wet insulation often causes roofing fasteners to corrode and reduces the performance of the roof.
- Trapped moisture can accelerate the deterioration of the building’s structural integrity.
- Wet insulation will degrade the roofing system.
- Wet insulation adds unnecessary weight to the building.
Radiation Cooling
Everything radiates heat. The ground, for example, emits heat continuously to outer space while receiving energy from the sun. In the daytime, incoming solar energy exceeds the outgoing energy and the temperature of the ground surface rises. During the day, the sun emits energy onto the roof and into the roof substrate of buildings. At night, as there is no incoming solar energy and the ground continues to radiate away heat, its temperature falls. At night, the building roof radiates the heat back into space. This is called radiation cooling. Areas of the roof that are of a higher mass (wet) retain this heat longer than that of the lower mass (dry) areas. Infrared imagers can detect this heat and “see” the warmer, higher mass areas, during the “window” of uneven heat dissipation.
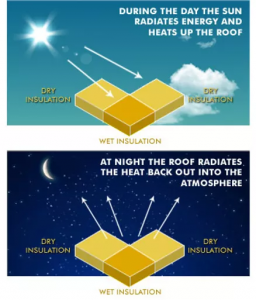
Infrared Thermography
Infrared Thermography, also known as an IR scan, is a non-destructive test method to detect and record temperature differences across the surface of an object. IR scans are the most common moisture detection method for identifying wet insulation on commercial roofing systems. During the day, wet insulation will absorb much more heat energy than dry insulation. At night, this heat is retained in the wet insulation longer and is released slower into the atmosphere. Most IR scans are done after sunset in order to capture this thermal signature of wet insulation trapped in a roofing system.
Solutions
There is a recognized three-stage approach to prevent wet insulation.
Stage No. 1: Design. When constructing a new building or remodeling an existing building, make sure it’s designed with attention to potential flaws and moisture sources. Specify insulation materials that are moisture resistant and control thermal bridging and condensation locations.
Stage No. 2: Construction. Pay attention to details. Inspect, verify, and manage latent moisture throughout construction.
Stage No. 3: Maintenance. Use qualified professionals and establish an annual routine inspection for copings at the top of parapet walls, visible flashings, lintels over windows, and control joint seals in masonry walls. Inspect for internal clues of moisture (peeling finishes or discoloration in walls or floors). Unfortunately, water in insulation or wall systems is often not visible until it has already done damage. Wet drywall may not be noticed until discoloration and mold set in. Once those things appear, repair work may be very extensive. Including a drone and aerial thermal imaging in your preventative maintenance program will help you avoid costly repairs by identifying wet insulation that cannot otherwise be seen.
Knowing the sources, identifying the problems, and finding the solutions are all important to keep your insulation dry.